(514) 993-8699

Lorenzo Mercuri-Bastien
My Mechanical Engineering Portfolio
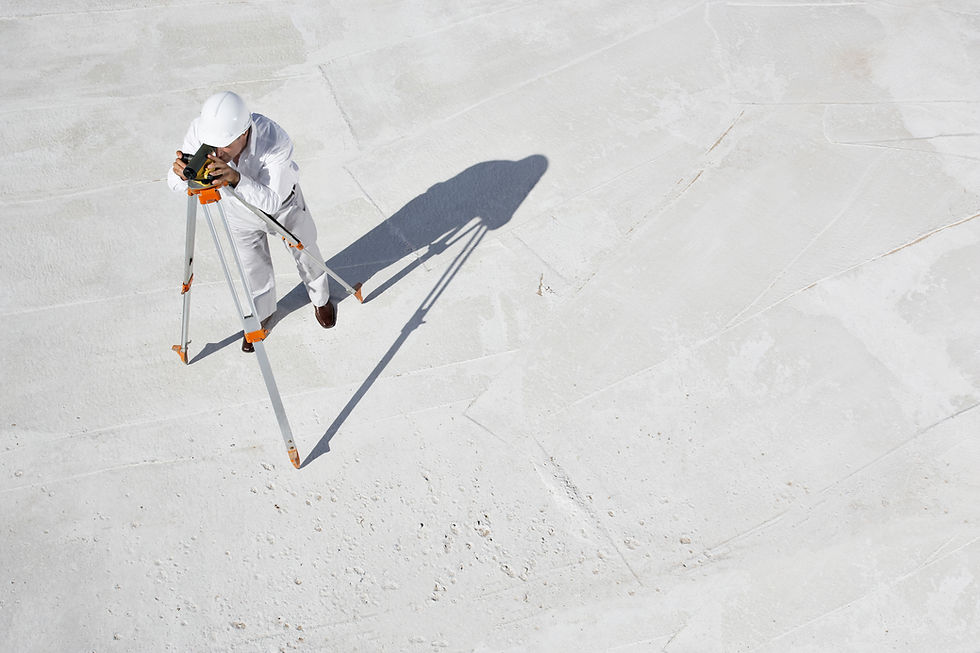
Bio
Personal Profile
I have a great passion for learning about the research and manufacturing that goes into the development mechanical designs. I have a bachelor degree in science specializing in Kinesiology and I currently graduated in Mechanical Engineering, with a goal of focusing on mechanical design in the near future.
Since I realized my passion for science and engineering, I knew I wanted to be involved in developing technology that would help humanity in some way. I am very inquisitive and eager to learn about new upcoming scientific discoveries and technological innovations. The idea of improving my knowledge by learning from previous innovations and scientific discoveries in order to build more sophisticated technology is an exciting thought to have. My curiosity led me to projects such as the Space Concordia Rover challenge where I contributed as a mechanical designer. From this experience I learned about the fundamental technical aspects involved in mechanical design such as the awareness of designing an assembled part that can be easily machined while in the process of improving my computer aided design skills with Solidworks. The experience also highlighted the importance of clear communication which fostered great team work. In the summer of 2019 I was accepted to do NSERC USRA research which involved fluid dynamics on the topic of Blunt Traumatic Aortic Rupture. During my experience as a research assistant I was fortunate to work with dedicated people within the field who taught me how to extract pertinent scientific data and also how to effectively communicate my results to a reader with the use of the Matlab software.
I look forward to continue enriching my knowledge with the aim of contributing to the development of science and technology.
Projects
Showcase of Work
Below is a showcase of all the projects I have done up to date during my years as a mechanical engineering student at Concordia University. The projects involve computer aided design with Solidworks, Ansys (finite element analysis) along with Matlab and Arduino softwares which utilize C++ and C programming languages.

Mini Capstone Project
The objective for this project was to design a foot actuated watercraft that could operate for 10 years while being used for 10 hours per day without failure. The watercraft also had to be used in warm conditions such as Florida. The watercraft had to be designed so that its maximum speed would remain within 12 km/hr and 20 km/hr. Due to these requirements it was crucial that fatigue analysis had to be conducted on the spur gears and shafts of the watercraft. The Solidworks software was used to generate CADs/drawings and the Matlab software was used for the calculations as shown below.

Steam Car Project
The challenge was to show that the steam car could travel at least 1 meter within 15 minutes without external forces other than the use of an air compressor steam simulation and boiler setup in order to power the vehicle. The material that was used was 3D printed ABS due to its high strength and light weight characteristics. For the transmission, the gear ratio was designed to get the highest torque output possible at the front shaft in order to overcome the steam car's inertia off the starting line.

Gyroscope Project
Initially, aluminum stock materials were given and the objective was to first design all the necessary parts with the Solidworks CAD software. After the designs of the parts were completed, process sheets were written in order to demonstrate the sequence of machining steps required to obtain the final product. The machine process involved the use of the milling press, drill press and lathe machine.

Space Concordia Rover Project
The requirements for the gripper assembly were to be able to grasp large and small objects while also being able to execute fine intricate movements in order to type on a keyboard. The prototype was first designed with the CAD software Solidworks and was then 3D printed with ABS filament. After being 3D printed, the gripper prototype was tested on a testing panel in order to test its gripping functionality with objects of various shapes.

Robotic Running Back Project
The tasks that my robot (NFL running back) performs are obstacle avoidance and light evasion. An ultrasonic sensor, a light sensor, two continuous servo motors and a pivot wheel were used. The ultrasonic sensor was placed on the front of the robot in order to detect an object at a specific distance. Once the specific distance was met, it would take a sharp right turn followed by a sharp left turn by rotating the two front wheels in opposite directions. A light sensor was placed on top of the robot and was oriented in the same direction as the ultrasonic sensor. When the light intensity changed, the sensor detected the change in voltage. Once the voltage was within a certain range, the robot would either take a slight left or right turn by rotating one of the front wheels slower than the other, with both wheels still rotating in the same direction. The programming was done with the use of an Arduino software IDE which utilizes C and C++ programming languages.

NSERC USRA Research Project
Data was retrieved from a previous experiment with the intention of improving upon the amount of relevant information that could be extracted from it.The experiment consisted of a cart that slid down a guide system and once the required speed was reached it then decelerated to a stop due to the deceleration system. Eight cases were analyzed at a speed of 40%, 55% and 70% of a maximum cart speed of 10m/s. At the point of impact, a high speed camera was placed and a laser shined through the fabricated silicone aorta in order to conduct particle image velocimetry. Particle image velocimetry is a non-intrusive laser optical measurement technique which allows for a velocity field to be obtained by tracking the motion of the particles placed in the fluid. The velocity field was then filtered with the use of MATLAB and pertinent fluid mechanics data was extracted from the fluid inside of the aorta during impact such as relative velocity, kinetic energy and vorticity. Pertinent data concerning mechanical deformation of the aortic wall were also extracted such as strain rate and percent elongation.
​
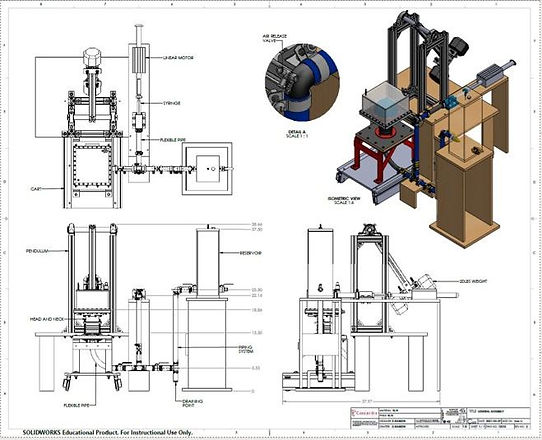
Capstone Project
The In-vitro Sub-Concussion Impulse Impact Experiment abbreviated to IVCIE is a project to study and gather data by simulating concussive and sub-concussive traumas using various equipment such as Particle Imagery Velocimetry measurement (PIV) device, CCD cameras, accelerometer and various other sensors. The system comprises of three parts; the first part consists of placing a synthetic adult sized human brain within a human sized acrylic dome which will simulate the skull and it will be placed on a constructed biofidelic neck. The other part of the design consists of a pendulum hitting the synthetic human brain structure, thus imitating a sub-concussive impact. The last part of the design consists of the reservoir and piping system. This will provide the required hydrostatic pressure and a specific pressure fluctuation of the CSF Fluid that surrounds the brain.

NSERC USRA Research Project
The objective of this project was to determine the geometric stiffness contour pattern of a 3D printed structural steel material with varying geometric shapes based on certain boundary conditions which is important considering that areas of higher geometric stiffness will experience higher residual stresses. The Ansys Mechanical APDL user interface was used to run the nodal displacement and the geometric stiffness simulations for each model.
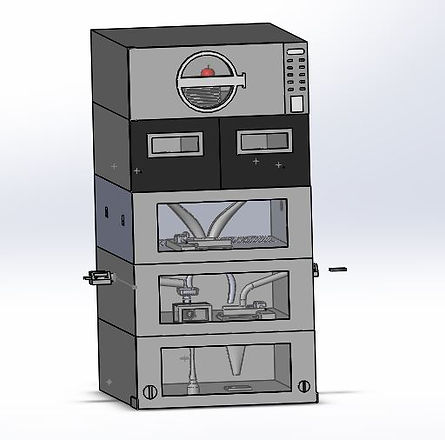
Deep Space Food Challenge
The challenge for this deep space food competition is to create a novel food production technology or system that requires minimal inputs and maximizes safe, nutritious, and palatable food outputs for long-duration space missions, and which have potential to benefit people on Earth. With the recent push for space flight to the moon and Mars astronauts will need a way to store and preserve their food for long space missions therefore the demand for novel food technology is very high. The Solidworks CAD software was utilized in order to produce the full assembly of the food machine.

Project 1.0: Micro2
Project 1.0: Micro2 is project that was designed in order to acquire a better understanding of the human immune system due to change induced by reduced gravity as well as stress on genes from hypergravity. Our experiment will first be done on the ground followed by an experiment done in a parabolic flight. Ultimately, for the final experiment our Micro2 design will be the payload within the Space Concordia rocket which will be sent into space for the purpose of collecting data. This data will provide a better understanding of the human immune system mechanisms that occur for astronauts during their missions to space.

Soft Shell Design for NFL Football Helmet Project
The Soft Shell NFL football helmet is a project that involves gathering data and designing a NFL football helmet to reduce the impact force experienced by NFL football players that can cause concussions. Tools such as Ansys (computer simulation), Solidworks (computer aided design) and matlab/excel (programming softwares) will be utilized to design the soft shell helmet.
Heading 1
My Mini Capstone Project
Foot Actuated watercraft

MATLAB Files
Project Calculations
Steam Car Project

Gyroscope Project

Gripper Project
Robotic Running Back Project
Blunt Traumatic Aortic Rupture
Case six: Aorta traveling at 55% of max velocity (10m/s)
The video below is the sixth case of the blunt traumatic aortic rupture experiment which demonstrates the fluid flow within a fabricated silicone aortic artery upon crash impact.
​
Capstone Project
In-Vitro Sub-Concussion Impulse Impact
​

Stiffness Modeling for Metal Additive Manufacturing
Ansys Mechancial APDL Simulation
The tool that was utilized to simulate geometric stiffness contours was the Ansys simulation software, specifically the Mechanical APDL user interface. The Ansys parametric design language (APDL) is a powerful scripting language which provides the capability to fully customize structural models and perform structural analysis operations. The modeling and structural analysis were completely done in the Ansys Mechanical APDL user interface due to the fairly simple geometric shapes that were used in the project. The stiffness modeling in Ansys mechanical APDL user interface will provide more insight into the compromised mechanical properties of metallic parts that are created from additive manufacturing approaches. A more detailed description of the methodology taken to create the simulation can be found in the Stiffness Modeling for Metal Additive Manufacturing Report.

Excel Geometric Stiffness Calculation Files
Imported Nodal Displacement data from Ansys Mechanical APDL user interface into excel in order to calculate the geometric stiffness of each model.
​
Available for Download
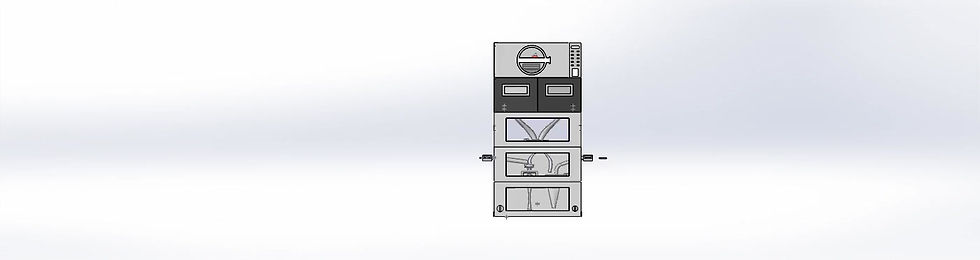
Deep Space Food Challenge
Full Assembly Food Machine
Food Challenge


Fifth_Sub_Assembly
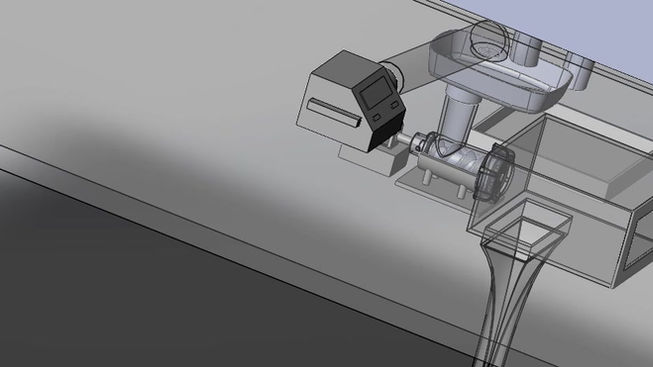
Fourth_Sub_Assembly_Mechanism

Fourth_Sub_Assembly_Mechanism

Fourth_Sub_Assembly_Mechanism

Project 1.0: Micro2
Simulation of Human Immune System in Micro Gravity
Soft Shell Design for NFL Helmet Project

Abstract Publications
View Now